Crack propagation in a plate with a hole simulated using XFEM Crack propagation in a plate with a hole simulated using XFEMThis example verifies and illustrates the use of the extendedfinite element method ( XFEM) inAbaqus/Standardto predict crack initiation and propagation due to stress concentration in aplate with a hole.Both the XFEM-based cohesive segments method and the XFEM-based linear elastic fracture mechanics( LEFM) approach are used to analyze thisproblem. The specimen is subjected to pure Mode I loading. In some casesdistributed pressure loads are applied to the cracked element surfaces as thecrack initiates and propagates in the specimen. The results presented arecompared to the available analytical solution. In addition, the same model isanalyzed using the XFEM-based low-cycle fatigue ( LCF)criterion to assess the fatigue life when the model is subjected tosub-critical cyclic loading.The following topics are discussed:. A plate with a circular hole is studied. The specimen, shown in,has a length of 0.34 m, a thickness of 0.02 m, a width of 0.2 m, and a holeradius of 0.02 m, under pure Mode I loading.defines the dimensions used to calculate the variation of crack length,a + c b:a is the crack length, b is half thespecimen width, and c is the hole radius.Equal and opposite displacements are applied at both ends in thelongitudinal direction.
The maximum displacement value is set equal to 0.00055m. To examine the mesh sensitivity, three different mesh discretizations of thesame geometry are studied.
Symmetry conditions reduce the specimen to a halfmodel. The original mesh, as depicted in,has 2060 plane strain elements. The second mesh has four times as many elementsas the original one, while the third mesh has sixteen times as many elements asthe original one.In the low-cycle fatigue analysis, two steps are involved. A static step isused to nucleate a crack at the site of stress concentration prior to thelow-cycle fatigue direct cyclic step, in which a cyclic distributed loadingwith a peak value of 1.25 MPa is specified. Three different meshdiscretizations of the same geometry are studied.
The second mesh has twice asmany elements as the original mesh, while the third mesh has four times as manyelements as the original mesh.The material data for the bulk material properties in the enriched elementsare E = 3.24GPa and ν= 0.3.The response of cohesive behavior in the enriched elements in the model isspecified. The maximum principal stress failure criterion is selected fordamage initiation, and an energy-based damage evolution law based on a BK law criterion is selected for damage propagation. The relevantmaterial data are as follows: σ m a x = 22.0MPa, G 1 C = 2.87× 10 3 N/m, G 2 C = 2.87× 10 3 N/m, and η = 1.0.The relevant material data defined above are also used in the model simulatedusing the XFEM-based LEFM approach. When thelow-cycle fatigue analysis using the Paris law is performed, the additionalrelevant data are as follows: c 1 = 0.5,c 2 = - 0.1,c 3 = 4.88× 10 −6, c 4 = 1.15,G t h r e s h G C = 0.001,and G p l G C = 0.85. Shows plots of the prescribed displacement versus the corresponding reactionforce with different mesh discretizations when the XFEM-based cohesive segments method is used.
The figure clearlyillustrates the convergence of the response to the same solution with meshrefinement. A plot of the applied stress versus the variation of crack lengthis presented inand compared with the results obtained by using the XFEM-based LEFM approach as well asthe analytical solution of. The agreement is better than 10% except when the cracklength is small, in which case the stress singularity ahead of the crack is notconsidered by the XFEM approach.
However, as indicated in this figure, the crackinitiates (i.e., a = 0)when the applied stress, σ,reaches a level of 8.37 MPa, giving a ratio of σ m a x σequal to 2.63. This value is in close agreement with the stress concentrationfactor of 2.52 obtained analytically for the same geometry. In addition, theresults in terms of crack length versus the cycle number obtained using thelow-cycle fatigue criterion inAbaqusare compared with the theoretical results in.Reasonably good agreement is obtained.
Defining initially bonded crack surfacesPotential crack surfaces are modeled as slave and master contact surfaces (see ). Any contact formulation except the finite-sliding, surface-to-surface formulation can be used. The predetermined crack surfaces are assumed to be initially partially bonded so that the crack tips can be identified explicitly by ABAQUS/Standard.
Initially bonded crack surfaces cannot be used with self-contact.Define an initial condition to identify which part of the crack is initially bonded. You specify the slave surface, the master surface, and a node set that identifies the initially bonded part of the slave surface. The unbonded portion of the slave surface will behave as a regular contact surface. Either the slave surface or the master surface must be specified; if only the master surface is given, all of the slave surfaces associated with this master surface that have nodes in the node set will be bonded at these nodes.If a node set is not specified, the initial contact conditions will apply to the entire contact pair; in this case, no crack tips can be identified, and the bonded surfaces cannot separate.If a node set is specified, the initial conditions apply only to the slave nodes in the node set. ABAQUS/Standard checks to ensure that the node set defined includes only slave nodes belonging to the contact pair specified.By default, the nodes in the node set are considered to be initially bonded in all directions.
Bonding only in the normal directionIt is possible to bond the nodes in the node set (or the contact pair if a node set is not defined) only in the normal direction. In this case the nodes are allowed to move freely tangential to the contact surfaces. Friction cannot be specified if the nodes are bonded only in the normal direction.Bonding only in the normal direction is typically used to model bonded contact conditions in Mode I crack problems where the shear stress ahead of the crack along the crack plane is zero.
Activating the crack propagation capabilityThe crack propagation capability must be activated within the step definition to specify that crack propagation may occur between the two surfaces that are initially partially bonded. You specify the surfaces along which the crack propagates.If the crack propagation capability is not activated for partially bonded surfaces, the surfaces will not separate; in this case the specified initial contact conditions would have the same effect as that provided by the tied contact capability, which generates a permanent bond between two surfaces during the entire analysis (see ). Propagation of multiple cracksCracks can propagate from either a single crack tip or multiple crack tips. The crack propagation capability in ABAQUS/Standard requires that the surfaces be initially partially bonded so that the crack tips can be identified. A contact pair can have crack propagation from multiple crack tips.

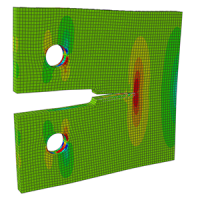
Crack Simulation With Abaqus
However, only one crack propagation criterion is allowed for a given contact pair. Crack propagation along several contact pairs can be modeled by specifying multiple crack propagation definitions. Specifying a debonding amplitude curveAfter debonding, the traction between two surfaces is initially carried as equal and opposite forces at the slave node and the corresponding point on the master surface. You can define how this force is to be reduced to zero with time after debonding starts at a particular node on the bonded surface.
You specify a relative amplitude, a, as a function of time after debonding starts at a node. Thus, suppose the force transmitted between the surfaces at slave node N is when that node starts to debond, which occurs at time. Then, for any time the force transmitted between the surfaces at node N is. The relative amplitude must be 1.0 at the relative time 0.0 and must reduce to 0.0 at the last relative time point given.The best choice of the amplitude curve depends on the material properties, specified loading, and the crack propagation criterion. If the stresses are removed too rapidly, the resulting large changes in the strains near the crack tip can cause convergence difficulties. For large-strain problems severe mesh distortion can also occur. For problems with rate-independent materials a linear amplitude curve is normally adequate.
For problems with rate-dependent materials the stresses should be ramped off more slowly at the beginning of debonding to avoid convergence and mesh distortion difficulties. Reducing the debond stress 25% in 50% of the time to debond will usually avoid problems.
The solution should not be strongly influenced by the details of the unloading procedure; if it is, this usually indicates that the mesh should be refined in the debond region.Once complete debonding has occurred at a point, the bond surfaces act like standard contact surfaces with associated interface characteristics. Where is the normal component of stress carried across the interface at the distance specified; and are the shear stress components in the interface; and and are the normal and shear failure stresses, which you must specify.
The second component of the shear failure stress, is not relevant in a two-dimensional analysis; therefore, the value of need not be specified. The crack-tip node debonds when the fracture criterion, f, reaches the value 1.0.If the value of is not given or is specified as zero, it will be taken to be a very large number so that the shear stress has no effect on the fracture criterion.The distance ahead of the crack tip is measured along the slave surface, as shown in.
The stresses at the specified distance ahead of the crack tip are obtained by interpolating the values at the adjacent nodes. The interpolation depends on whether first-order or second-order elements are used to define the slave surface. Where is the measured value of crack opening displacement and is the critical value of the crack opening displacement (user-specified). The crack-tip node debonds when the fracture criterion reaches the value 1.0.You must supply the crack opening displacement versus cumulative crack length data. In ABAQUS/Standard the cumulative crack length is defined as the distance between the initial crack tip and the current crack tip measured along the slave surface in the current configuration.
The crack opening displacement is defined as the normal distance separating the two faces of the crack at the given distance.You specify the position, n, behind the crack tip where the critical crack opening displacement is calculated. The value of this position must be specified as the length of the straight line joining the current crack tip and points on the slave and master surfaces.
Crack length versus time criterionTo specify the crack propagation explicitly as a function of total time, you must provide a crack length versus time relationship and a reference point from which the crack length is measured. This reference point is defined by specifying a node set.
ABAQUS/Standard finds the average of the current positions of the nodes in the set to define the reference point. During crack propagation the crack length is measured from this user-specified reference point along the slave surface in the deformed configuration.
The time specified must be total time, not step time.The fracture criterion, f, is stated in terms of the user-specified crack length and the length of the current crack tip. The length of the current crack tip from the reference point is measured as the sum of the straight line distance of the initial crack tip from the reference point and the distance between the initial crack tip and the current crack tip measured along the slave surface.Referring to, let node 1 be the initial location of the crack tip and node 3 be the current location of the crack tip. The distance of the current crack tip located at node 3 is given.
Where l is the length at the current time obtained from the user-specified crack length versus time curve. Crack-tip node 3 will debond when the failure function f reaches the value of 1.0 (within the user-defined tolerance).If geometric nonlinearity is considered in the step , the reference point may move as the body deforms; you must ensure that this movement does not invalidate the crack length versus time criterion.ABAQUS/Standard does not extrapolate beyond the end points of your crack data. Therefore, if the first crack length specified is greater than the distance from the crack reference point to the first bonded node, the first bonded node will never debond and the crack will not propagate. In this case ABAQUS/Standard will print warning messages in the message (.msg) file.
Controlling time incrementation during debondingWhen automatic incrementation is used, you can specify the size of the time increment used just after debonding starts. By default, the time increment is equal to the last relative time specified. However, if a fracture criterion is met at the beginning of an increment, the size of the time increment used just after debonding starts will be set equal to the minimum time increment allowed in this step.For fixed time incrementation the specified time increment value will be used as the time increment size after debonding starts if ABAQUS/Standard finds it needs a smaller time increment than the fixed time increment size. The time increment size will be modified as required until debonding is complete.Although temperature is not a degree of freedom in stress/displacement elements, nodal temperatures can be specified as predefined fields.
The specified temperature affects temperature-dependent critical stress and crack opening displacement failure criteria, if specified.The values of user-defined field variables can be specified. These values affect field-variable-dependent critical stress and crack opening displacement failure criteria, if specified.In ABAQUS/Standard the temperatures and user-defined field variables on slave and master surfaces are averaged to determine the critical stresses and crack opening displacements. Contour integralsContour integrals can be requested for two-dimensional crack propagation analysis. If the contours are chosen so that the crack tip passes through the contour, the contour value will go to zero (as it should). Therefore, in crack propagation analysis contour integrals should be requested far enough from the crack tip that the crack tip does not pass through the contour, which is easily done by including all nodes along the bond surface in the crack-tip node set specified. See, for details on contour integral output.